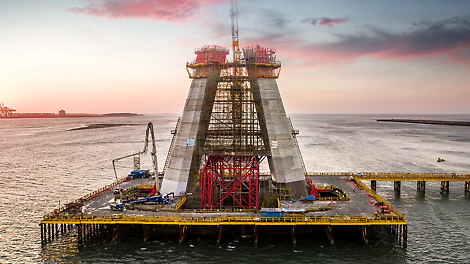
Accompany us to the Danjiang bridge
On our journey towards Danjiang Bridge, we cross the Tamsui River, which meanders through Taipei. At the mouth of the river in the north of the city, the bridge is rapidly approaching. The project is not only of particular importance to us and our client Kung Sing Engineering, but also to the residents of Taipei itself. The Danjiang Bridge, designed by Zaha Hadid, will connect the industrial zones of Tamsui and the Bali District opposite, which will lead to improved infrastructure and relieve traffic congestion in the region. The imposing structure will also become a new landmark for the city. A central element of the bridge is the imposing pylon that supports the structure and characterises its futuristic silhouette.
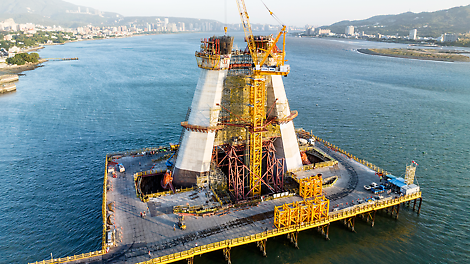
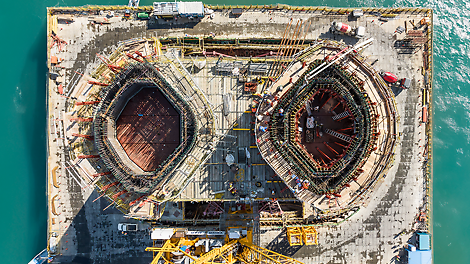
Customised formwork solutions for complex requirements
The challenges involved in a project of this size are enormous. The complex shape of the pylon requires customised formwork solutions as well as great precision and expertise. When we arrive at the construction site, we meet our supervisor Gopi, who plays a crucial role in the realisation of the Danjiang Bridge. With his expertise and experience, he makes a significant contribution to the smooth running of the construction site and the acceleration of construction progress. As we walk round the pylon, he explains the special project requirements. ‘The pylon is shaped like an upside-down Y, gets narrower and narrower and curves outwards at the bottom and inwards at the top. All of this makes its shape so unusual and complex at the same time,’ says Gopi. This changing shape posed the greatest challenge and was the reason why the pylon was divided into 53 concreting sections.
Our engineers therefore developed special 3D free-form moulds for the different sections, which adapt to the geometry of the pier. In addition, our VARIO formwork was used in combination with our climbing systems. The advantage: both systems can be flexibly combined with each other and adapt to the unusual shape.
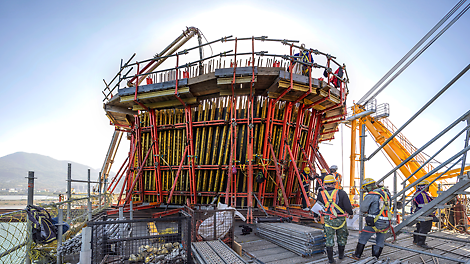
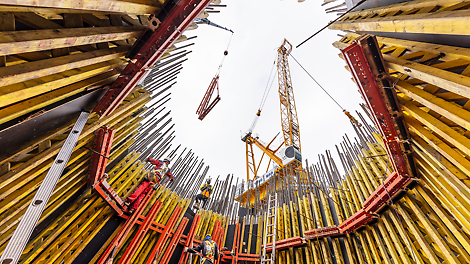
‘For the first 29 sections above the water surface, the construction team has already been able to efficiently form the pier with our VARIO GT 24 girder wall formwork and our SCS climbing system,’ explains Gopi. The concreting of the upper sections is currently taking place. Here too, the VARIO formwork is forming the basis due to its ability to pour up to 18 metres in one go. What we immediately notice is that it is no longer the SCS but the ACS climbing system that can be seen. Gopi knows why: ‘SCS is great for inclined shapes like the feet of the pylon. Our ACS self-climbing system, on the other hand, can climb straight parts most efficiently on rails and is therefore better suited for the upper area. However, both systems have one thing in common: At these great heights, they offer workers a high level of safety.’
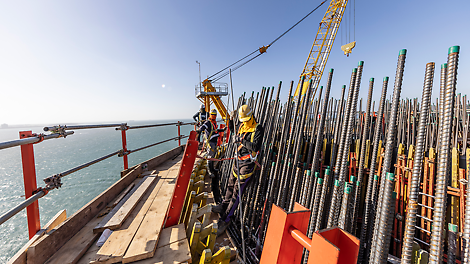
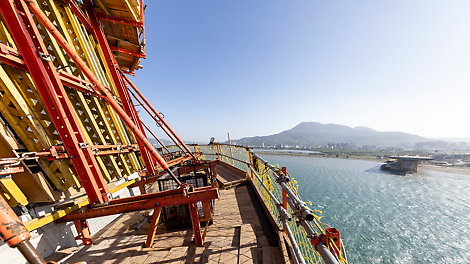
Always a competent partner – from planning to support
Another special feature: thanks to the use of our systems, the sections can be completed within 17 days - to the complete satisfaction of site manager Zeng Wei-Cheng. We also meet him during our tour. In conversation, he reveals what impresses him about PERI: ‘The efficiency of the formwork systems is consistently high, so that our requirements in terms of project progress are fully met. In addition, the work requires special attention to the occupational safety of the site personnel. And PERI has already taken this into account in the formwork planning.’ Another highlight: the intensive project support from Gopi. Thanks to this, the assembly team knew how to set up and operate our systems in the shortest possible time. At the same time, it makes it clear how valuable the symbiosis of the right systems, good advice and close communication between the parties involved are for this extraordinary project.
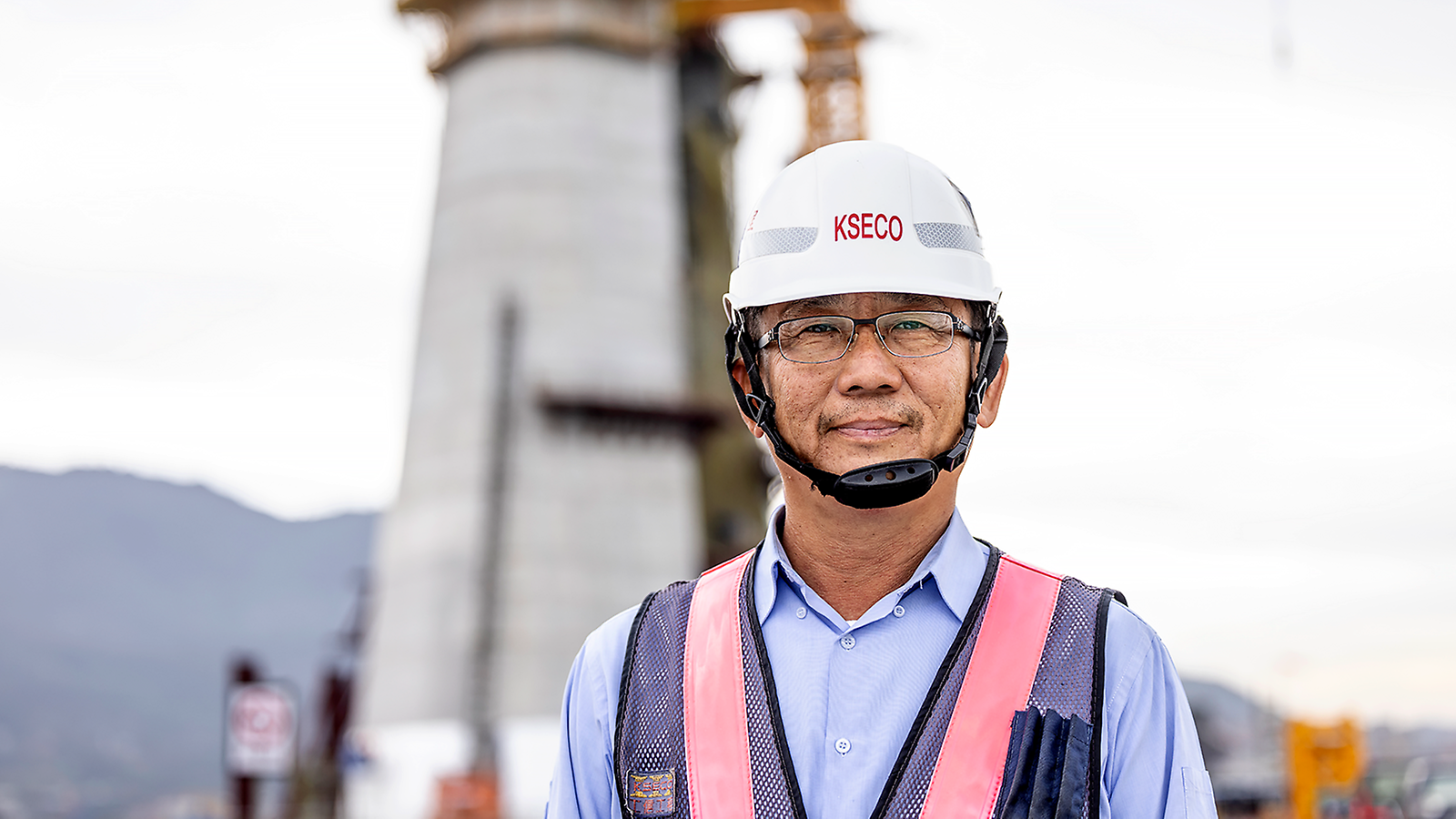
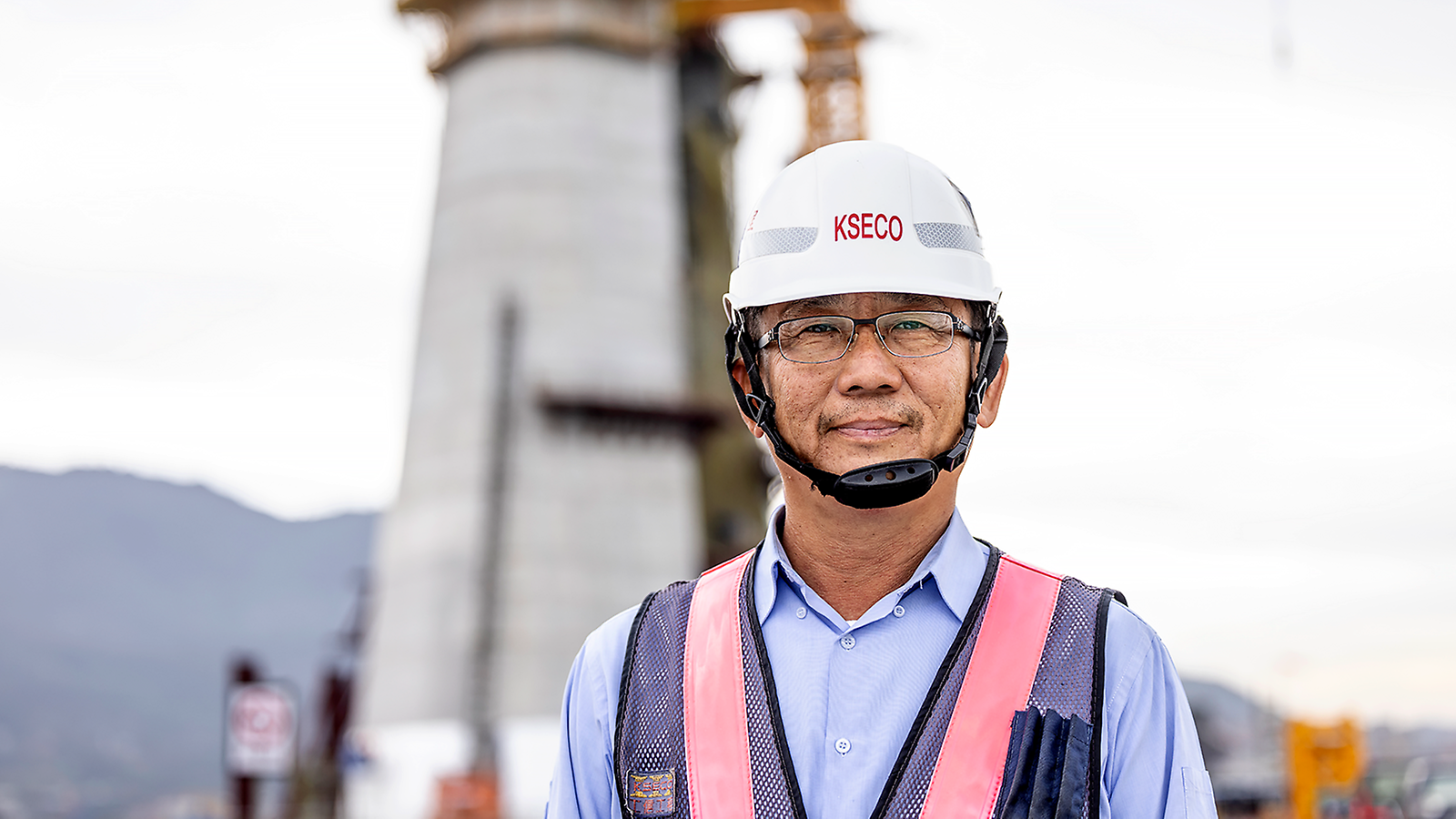
We are on site for you worldwide
Our support knows no borders - no matter where you are in the world. Simply select the website for your country and discover detailed information about our products, projects and contact details for our local contacts. We are always happy to assist you and look forward to helping you too.