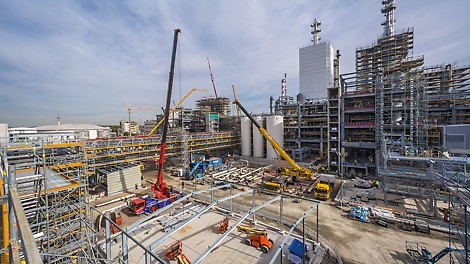
Scaffolding Solutions for Industrial Applications
PERI Systems and Services for Industrial Construction and Plant Construction
Join us on a journey through a portfolio that spans continents and highlights the adaptability and reliability of PERI UP industrial scaffolding solutions. As a trusted partner to the scaffolding industry, PERI is proud to showcase a range of international projects that exemplify innovation, efficiency and safety on a global scale.
The new plant is expected to increase BASF’s annual production capacity for vitamin A by 1,500 t. Around 600 machines and devices as well as 5,000 test points were integrated into the process control system. In addition, 250 linear metres of pipe bridges had to be constructed.
At peak times, around 1,300 t of PERI system material were in use at the same time. It was possible to use the PERI solutions in an extremely versatile manner, for example for standing scaffolds, safety scaffolds, suspended scaffolds, shoring, stairs, material platforms and mobile working scaffolds. Most notably, by combining the PERI UP Scaffolding Kit with the VARIOKIT Engineering Construction Kit, it was possible to ensure both geometric and static flexibility thanks to the metric basic grid of both systems – and thus the highest degree of working safety.
At peak times, around 1,300 t of PERI system material were in use at the same time. It was possible to use the PERI solutions in an extremely versatile manner, for example for standing scaffolds, safety scaffolds, suspended scaffolds, shoring, stairs, material platforms and mobile working scaffolds. Most notably, by combining the PERI UP Scaffolding Kit with the VARIOKIT Engineering Construction Kit, it was possible to ensure both geometric and static flexibility thanks to the metric basic grid of both systems – and thus the highest degree of working safety.
At peak times, around 1,300 t of PERI system material were in use at the same time. It was possible to use the PERI solutions in an extremely versatile manner, for example for standing scaffolds, safety scaffolds, suspended scaffolds, shoring, stairs, material platforms and mobile working scaffolds. Most notably, by combining the PERI UP Scaffolding Kit with the VARIOKIT Engineering Construction Kit, it was possible to ensure both geometric and static flexibility thanks to the metric basic grid of both systems – and thus the highest degree of working safety.
At peak times, around 1,300 t of PERI system material were in use at the same time. It was possible to use the PERI solutions in an extremely versatile manner, for example for standing scaffolds, safety scaffolds, suspended scaffolds, shoring, stairs, material platforms and mobile working scaffolds. Most notably, by combining the PERI UP Scaffolding Kit with the VARIOKIT Engineering Construction Kit, it was possible to ensure both geometric and static flexibility thanks to the metric basic grid of both systems – and thus the highest degree of working safety.
At peak times, around 1,300 t of PERI system material were in use at the same time. It was possible to use the PERI solutions in an extremely versatile manner, for example for standing scaffolds, safety scaffolds, suspended scaffolds, shoring, stairs, material platforms and mobile working scaffolds. Most notably, by combining the PERI UP Scaffolding Kit with the VARIOKIT Engineering Construction Kit, it was possible to ensure both geometric and static flexibility thanks to the metric basic grid of both systems – and thus the highest degree of working safety.
At peak times, around 1,300 t of PERI system material were in use at the same time. It was possible to use the PERI solutions in an extremely versatile manner, for example for standing scaffolds, safety scaffolds, suspended scaffolds, shoring, stairs, material platforms and mobile working scaffolds. Most notably, by combining the PERI UP Scaffolding Kit with the VARIOKIT Engineering Construction Kit, it was possible to ensure both geometric and static flexibility thanks to the metric basic grid of both systems – and thus the highest degree of working safety.
With its capacity of 1,320 MW, ISKEN is one of the largest coal-fired power plants in the country, generating energy for a significant part of Turkey.
Recurring maintenance work is one of the tasks carried out regularly at the large plant. This downtime calls for reliable and safe work processes. PERI provided support for these time-critical tasks with approx. 500 t of PERI UP scaffolding material, engineering services, planning support, and logistical and consulting services.
Recurring maintenance work is one of the tasks carried out regularly at the large plant. This downtime calls for reliable and safe work processes. PERI provided support for these time-critical tasks with approx. 500 t of PERI UP scaffolding material, engineering services, planning support, and logistical and consulting services.
Recurring maintenance work is one of the tasks carried out regularly at the large plant. This downtime calls for reliable and safe work processes. PERI provided support for these time-critical tasks with approx. 500 t of PERI UP scaffolding material, engineering services, planning support, and logistical and consulting services.
Recurring maintenance work is one of the tasks carried out regularly at the large plant. This downtime calls for reliable and safe work processes. PERI provided support for these time-critical tasks with approx. 500 t of PERI UP scaffolding material, engineering services, planning support, and logistical and consulting services.
Recurring maintenance work is one of the tasks carried out regularly at the large plant. This downtime calls for reliable and safe work processes. PERI provided support for these time-critical tasks with approx. 500 t of PERI UP scaffolding material, engineering services, planning support, and logistical and consulting services.
Recurring maintenance work is one of the tasks carried out regularly at the large plant. This downtime calls for reliable and safe work processes. PERI provided support for these time-critical tasks with approx. 500 t of PERI UP scaffolding material, engineering services, planning support, and logistical and consulting services.
The oil and gas field Ku-Maloob-Zaap (KMZ), which covers a total area of around 121 km², is situated in the bay of Campeche, 105 km north-east of the city of Ciudad del Carmen. In 2019, a new gas compressor platform named CA-KU-A1 was added to the oil and gas production complex that is located there. To carry out the time-critical construction project, PERI provided flexible scaffolding solutions and comprehensive on-site support.
With the aid of the modular PERI UP Scaffolding System, it was possible to erect safe working platforms even at great heights. Being able to change the direction of the decks within the scaffolding bays at will made it possible to build around obstructions such as pipelines or load-bearing constructions. This meant that working areas were almost completely free of gaps with no height offset or trip hazards. The self-securing ledger connection on the scaffolding node, the integrated lift lock on the non-slip decks and the end-to-end lateral protection provided a particularly high degree of safety.
With the aid of the modular PERI UP Scaffolding System, it was possible to erect safe working platforms even at great heights. Being able to change the direction of the decks within the scaffolding bays at will made it possible to build around obstructions such as pipelines or load-bearing constructions. This meant that working areas were almost completely free of gaps with no height offset or trip hazards. The self-securing ledger connection on the scaffolding node, the integrated lift lock on the non-slip decks and the end-to-end lateral protection provided a particularly high degree of safety.
With the aid of the modular PERI UP Scaffolding System, it was possible to erect safe working platforms even at great heights. Being able to change the direction of the decks within the scaffolding bays at will made it possible to build around obstructions such as pipelines or load-bearing constructions. This meant that working areas were almost completely free of gaps with no height offset or trip hazards. The self-securing ledger connection on the scaffolding node, the integrated lift lock on the non-slip decks and the end-to-end lateral protection provided a particularly high degree of safety.
With the aid of the modular PERI UP Scaffolding System, it was possible to erect safe working platforms even at great heights. Being able to change the direction of the decks within the scaffolding bays at will made it possible to build around obstructions such as pipelines or load-bearing constructions. This meant that working areas were almost completely free of gaps with no height offset or trip hazards. The self-securing ledger connection on the scaffolding node, the integrated lift lock on the non-slip decks and the end-to-end lateral protection provided a particularly high degree of safety.
With the aid of the modular PERI UP Scaffolding System, it was possible to erect safe working platforms even at great heights. Being able to change the direction of the decks within the scaffolding bays at will made it possible to build around obstructions such as pipelines or load-bearing constructions. This meant that working areas were almost completely free of gaps with no height offset or trip hazards. The self-securing ledger connection on the scaffolding node, the integrated lift lock on the non-slip decks and the end-to-end lateral protection provided a particularly high degree of safety.
With the aid of the modular PERI UP Scaffolding System, it was possible to erect safe working platforms even at great heights. Being able to change the direction of the decks within the scaffolding bays at will made it possible to build around obstructions such as pipelines or load-bearing constructions. This meant that working areas were almost completely free of gaps with no height offset or trip hazards. The self-securing ledger connection on the scaffolding node, the integrated lift lock on the non-slip decks and the end-to-end lateral protection provided a particularly high degree of safety.
The 90-m-high „flare”, one of the landmarks of the Leuna industrial site and a safety-relevant element of the DOMO Chemicals production plant, was refurbished.
Working and safety scaffolds were used for extensive corrosion prevention and insulation work. The benefit: safe workplaces for all works carried out as well as simplification of planning and assembly work due to the compatibility of modular systems and the use of standardised connecting parts.
Working and safety scaffolds were used for extensive corrosion prevention and insulation work. The benefit: safe workplaces for all works carried out as well as simplification of planning and assembly work due to the compatibility of modular systems and the use of standardised connecting parts.
Working and safety scaffolds were used for extensive corrosion prevention and insulation work. The benefit: safe workplaces for all works carried out as well as simplification of planning and assembly work due to the compatibility of modular systems and the use of standardised connecting parts.
Working and safety scaffolds were used for extensive corrosion prevention and insulation work. The benefit: safe workplaces for all works carried out as well as simplification of planning and assembly work due to the compatibility of modular systems and the use of standardised connecting parts.
Working and safety scaffolds were used for extensive corrosion prevention and insulation work. The benefit: safe workplaces for all works carried out as well as simplification of planning and assembly work due to the compatibility of modular systems and the use of standardised connecting parts.
Working and safety scaffolds were used for extensive corrosion prevention and insulation work. The benefit: safe workplaces for all works carried out as well as simplification of planning and assembly work due to the compatibility of modular systems and the use of standardised connecting parts.
Certification tests were conducted on the new Airbus A350 XWB wide-body aircraft within a specially designed testing hangar.
A scaffolding solution, comprising PERI UP and VARIOKIT components, was employed for test preparations, continuous measurement, and inspection work, simulating an impressive 86,400 flights. The benefit: optimum adaptation of the working levels to the fuselage and wing, taking into account the steel and hydraulic structures and the traffic routes that needed to be kept clear, as well as straightforward conversion in 25 cm increments.
A scaffolding solution, comprising PERI UP and VARIOKIT components, was employed for test preparations, continuous measurement, and inspection work, simulating an impressive 86,400 flights. The benefit: optimum adaptation of the working levels to the fuselage and wing, taking into account the steel and hydraulic structures and the traffic routes that needed to be kept clear, as well as straightforward conversion in 25 cm increments.
A scaffolding solution, comprising PERI UP and VARIOKIT components, was employed for test preparations, continuous measurement, and inspection work, simulating an impressive 86,400 flights. The benefit: optimum adaptation of the working levels to the fuselage and wing, taking into account the steel and hydraulic structures and the traffic routes that needed to be kept clear, as well as straightforward conversion in 25 cm increments.
A scaffolding solution, comprising PERI UP and VARIOKIT components, was employed for test preparations, continuous measurement, and inspection work, simulating an impressive 86,400 flights. The benefit: optimum adaptation of the working levels to the fuselage and wing, taking into account the steel and hydraulic structures and the traffic routes that needed to be kept clear, as well as straightforward conversion in 25 cm increments.
A scaffolding solution, comprising PERI UP and VARIOKIT components, was employed for test preparations, continuous measurement, and inspection work, simulating an impressive 86,400 flights. The benefit: optimum adaptation of the working levels to the fuselage and wing, taking into account the steel and hydraulic structures and the traffic routes that needed to be kept clear, as well as straightforward conversion in 25 cm increments.
A scaffolding solution, comprising PERI UP and VARIOKIT components, was employed for test preparations, continuous measurement, and inspection work, simulating an impressive 86,400 flights. The benefit: optimum adaptation of the working levels to the fuselage and wing, taking into account the steel and hydraulic structures and the traffic routes that needed to be kept clear, as well as straightforward conversion in 25 cm increments.
The Chevron Phillips U.S. Gulf Coast Petrochemicals Project in Baytown, Texas is a gigantic natural gas processing plant. When constructing the centerpiece of the complex, PERI ISP allowed the efficient use of large quantities of materials.
The Integrated Scaffold Programme (ISP) from PERI encompasses the 5D PERI Path software program and facilitates early cost estimates, operational planning and materials management as well as planning on-site material requirements in advance. In Baytown, the software monitored the use of around 750,000 scaffolding components and all related work considerations. The data allowed a detailed analysis of the working hours to be carried out and provided enormous transparency. As a result, it was possible to plan in more detail, reduce labour and logistics costs, and more effectively manage scaffolding operations.
The Integrated Scaffold Programme (ISP) from PERI encompasses the 5D PERI Path software program and facilitates early cost estimates, operational planning and materials management as well as planning on-site material requirements in advance. In Baytown, the software monitored the use of around 750,000 scaffolding components and all related work considerations. The data allowed a detailed analysis of the working hours to be carried out and provided enormous transparency. As a result, it was possible to plan in more detail, reduce labour and logistics costs, and more effectively manage scaffolding operations.
The Integrated Scaffold Programme (ISP) from PERI encompasses the 5D PERI Path software program and facilitates early cost estimates, operational planning and materials management as well as planning on-site material requirements in advance. In Baytown, the software monitored the use of around 750,000 scaffolding components and all related work considerations. The data allowed a detailed analysis of the working hours to be carried out and provided enormous transparency. As a result, it was possible to plan in more detail, reduce labour and logistics costs, and more effectively manage scaffolding operations.
The Integrated Scaffold Programme (ISP) from PERI encompasses the 5D PERI Path software program and facilitates early cost estimates, operational planning and materials management as well as planning on-site material requirements in advance. In Baytown, the software monitored the use of around 750,000 scaffolding components and all related work considerations. The data allowed a detailed analysis of the working hours to be carried out and provided enormous transparency. As a result, it was possible to plan in more detail, reduce labour and logistics costs, and more effectively manage scaffolding operations.
The Integrated Scaffold Programme (ISP) from PERI encompasses the 5D PERI Path software program and facilitates early cost estimates, operational planning and materials management as well as planning on-site material requirements in advance. In Baytown, the software monitored the use of around 750,000 scaffolding components and all related work considerations. The data allowed a detailed analysis of the working hours to be carried out and provided enormous transparency. As a result, it was possible to plan in more detail, reduce labour and logistics costs, and more effectively manage scaffolding operations.
The Integrated Scaffold Programme (ISP) from PERI encompasses the 5D PERI Path software program and facilitates early cost estimates, operational planning and materials management as well as planning on-site material requirements in advance. In Baytown, the software monitored the use of around 750,000 scaffolding components and all related work considerations. The data allowed a detailed analysis of the working hours to be carried out and provided enormous transparency. As a result, it was possible to plan in more detail, reduce labour and logistics costs, and more effectively manage scaffolding operations.
The mega project in southern Malaysia is expanding extremely quickly – likewise, the shoring and working scaffold of the cracking plant for heavy residue materials resulting from the first petroleum processing steps.
The 30 m high reactor tower is the highest part of the plant segment. The entire scaffolding system complete with shoring towers, access means and working levels was realized with PERI UP Scaffolding Kit. Fast assembly due to lightweight components and labour-saving connection technology with a high load-bearing capacity is one of the characteristics that qualify PERI UP as scaffolding for projects of this type.
The 30 m high reactor tower is the highest part of the plant segment. The entire scaffolding system complete with shoring towers, access means and working levels was realized with PERI UP Scaffolding Kit. Fast assembly due to lightweight components and labour-saving connection technology with a high load-bearing capacity is one of the characteristics that qualify PERI UP as scaffolding for projects of this type.
The 30 m high reactor tower is the highest part of the plant segment. The entire scaffolding system complete with shoring towers, access means and working levels was realized with PERI UP Scaffolding Kit. Fast assembly due to lightweight components and labour-saving connection technology with a high load-bearing capacity is one of the characteristics that qualify PERI UP as scaffolding for projects of this type.
The 30 m high reactor tower is the highest part of the plant segment. The entire scaffolding system complete with shoring towers, access means and working levels was realized with PERI UP Scaffolding Kit. Fast assembly due to lightweight components and labour-saving connection technology with a high load-bearing capacity is one of the characteristics that qualify PERI UP as scaffolding for projects of this type.
The 30 m high reactor tower is the highest part of the plant segment. The entire scaffolding system complete with shoring towers, access means and working levels was realized with PERI UP Scaffolding Kit. Fast assembly due to lightweight components and labour-saving connection technology with a high load-bearing capacity is one of the characteristics that qualify PERI UP as scaffolding for projects of this type.
The 30 m high reactor tower is the highest part of the plant segment. The entire scaffolding system complete with shoring towers, access means and working levels was realized with PERI UP Scaffolding Kit. Fast assembly due to lightweight components and labour-saving connection technology with a high load-bearing capacity is one of the characteristics that qualify PERI UP as scaffolding for projects of this type.
PERI Systems and Services for Industrial Construction and Plant Construction
You need a strong partner for your project? Simply visit the PERI website of your country and contact our local colleagues.