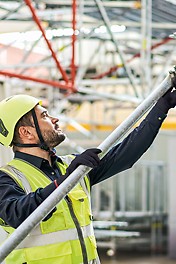
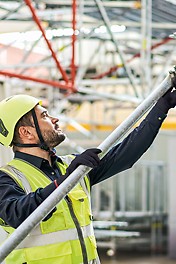
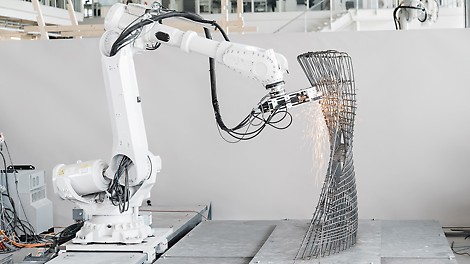
Download Press Release
The images in more detail
Sustainability plays an important role in the development of PERI products. That is why there is a separate area at this year's bauma dedicated solely to this topic. The formwork and scaffolding manufacturer, which has been climate-neutral since 2021, published its first sustainability report in the middle of this year. Sustainable operations has been the basis of PERI's business activities since the company was founded over 50 years ago. PERI is convinced that promoting sustainability contributes to the development and growth of the family-owned company and brings great added value for customers.
Facelift for the tried-and-tested MAXIMO Panel Formwork
Visitors to the PERI exhibition hall at the bauma can gain insight into the future of MAXIMO Panel Formwork. Thanks to a comprehensive facelift, the MAXIMO Panel Formwork now masters the balancing act between efficiency and sustainability for a wide range of applications. The MAXIMO frame has been optimised in terms of durability thanks to an improved profile and a modified lifting corner. In addition, an innovative and sustainable panel surface coating ensures holistic corrosion prevention and therefore an increased service life. The varied grid of MAXIMO with 30 cm and the PERI UP Scaffolding Kit with 25 cm will be bypassed in the future by the new functional brace. This means a wide variety of components can be flexibly connected to the MAXIMO panels. In doing so, PERI is taking another important step as a complete supplier of formwork and scaffolding from a single source.
In addition, PERI will present additional innovations to complement the proven MAXIMO Panel Formwork. As a result, MAXIMO can now be used even more flexibly with a new solution for designing an extremely wide variety of corner situations. The MAXIMO Shaft Corner is complemented by a new striking module that saves energy and enables efficient striking of the shaft corners. The low and compact construction as well as the ergonomic design also enable barrier-free work with fewer interference points than before. The hydraulic module can be easily attached to the shaft corners of MAXIMO and TRIO Panel Formwork and can be used with all standard PERI hydraulic units.
Resource-saving formlining insertion and replacement
The new and weather-resistant ROBU B Formwork Panel with an easy-to-repair surface and a correspondingly long service life is another PERI innovation. It is a sustainable formlining alternative for MAXIMO Wall Formwork and SKYDECK Panelised Slab Formwork. ROBU B combines the advantages of a wooden formwork panel with those of a polypropylene panel – the core is made of birch, while the concrete-facing side is made of a very robust polypropylene layer. The UV-resistant panel prevents discolouration of the concrete and can be marked and repaired directly on the construction site if necessary. Due to resource-efficient use of timber and its durability, it is one of many examples of the sustainability of PERI products.
PERI also gives insight into the future of formwork panels with the innovative Fast Panel Exchange System for MAXIMO Panel Formwork. Thanks to the modular use of three individual components – base support panel, sealing and formlining – changing the formlining on MAXIMO Panel Formwork will be particularly easy in the future, while saving resources at the same time. Since the load is transferred exclusively via the base support panel, the formlining for MAXIMO elements can be freely selected. This also enables particularly easy project-specific adaptation of the formwork elements and the production of individual concrete surfaces.
Digital management of construction projects with the new myPERI Customer Portal
Just in time for bauma 2022, the successful myPERI Customer Portal is taking another step into the future. With a new and future-proof platform and innovative features, it offers even more transparency and interactivity. The myPERI Customer Portal enables access to PERI construction projects with comprehensive project information on used and required materials, costs as well as product and article information. Reports and visual representations also facilitate work processes in all phases of construction site management. Important project data is also stored in a digitalised and centralised manner and can be used by all participants at the same time, which ensures transparent and simplified communication.
The revised user interface with responsive design for all end devices and the new search function ensure even more intuitive operation. This allows users to manage their construction projects digitally and track progress while on the move. PERI is constantly refining the portal together with its customers. More functions are in the planning phase, e.g. for reporting. The new myPERI has been available in Germany since September 2022 – other countries will be added on a gradual basis.
Innovative future-oriented thinking with MESH, 3D printing and sensor technology
When developing new products, PERI focuses not only on sustainability but also on the topic of digitalisation. For example with the innovative MESH technology, which PERI will present to interested visitors for the first time at bauma. The robot-assisted technology was developed at ETH Zurich and has been used in an industrial construction process in partnership with PERI and Sika since 2018. The next step followed this year with the founding of MESH AG, an ETH spin-off based in Zurich with the participation of PERI and Sika. The result is impressive: MESH is one of the finalists in the digitalisation category of the bauma Innovation Award.
MESH technology is a digital production method for reinforced concrete structures that makes it possible to produce complex or curved reinforcement cages, which were previously manufactured with elaborate manual work, through an automated prefabrication process. The 3D grid structure created in this way then serves as formwork and reinforcement at the same time and is filled with a specific concrete mix. This allows complex shapes and structures to be created cost-effectively without conventional formwork and without formwork waste. The MESH technology is used in customised concrete structures for the production of sophisticated shapes for building construction and civil engineering as well as for the structurally optimised creation of conventional concrete structures with less material input than usual.
With 3D Construction Printing, PERI has another innovation in its portfolio, to which almost 400 m2 are dedicated at this year's bauma. In the 3D printing area, visitors can look forward to a live demonstration of 3D Construction Printing with the COBOD BOD2. In printing technology, PERI relies on the COBOD BOD2 gantry printer from the Danish manufacturer and market leader COBOD, in which PERI has held a stake since 2018. Development of the technology has been ongoing since the last bauma and the design and technical options of 3D printing have been optimised. For the first time, the 3D printing team will present its extensive service portfolio at its own booth with an open area directly in front of the PERI exhibition hall.
Digital support during the concreting process is provided by the flexible sensor portfolio of PERI InSite Construction, which helps site personnel to make informed decisions about the concreting process. At bauma, PERI will be presenting the new ISC Hub for the first time, which will make data collection even easier from now on. The simple and handy control unit makes it possible to take several measurements and measurement types at once. While the SONO WZ Water-Content Analyser displays the measurement results directly on the hand-held device, the three sensors for monitoring concrete strength, concrete pressure and concrete detection are connected by cable to a reusable transmitter unit, the ISC Node, which communicates with the ISC Hub. The Hub in turn transmits the collected data to a cloud solution, where the user can retrieve it in real time. For optimised data collection during the entire concreting process, several nodes can be connected to the ISC Hub at the same time. At bauma, PERI experts will explain the functionality of the PERI InSite Construction portfolio on a replica of the piers and tunnel formwork carriage of the 485-m-long Filstal Bridge in Mühlhausen im Täle, Germany. This is part of the high-speed railway line between Wendlingen and Ulm and, at a height of 85 m, is one of the highest railway bridges in Germany, connecting the Bossler Tunnel in the north with the Steinbühl Tunnel in the south.
Innovations from the slab formwork sector
In addition to tried-and-tested PERI slab formwork, PERI will be presenting SKYMAX and ALPHADECK Panel Slab Formwork, which are additional innovative systems for different customer requirements.
The modular principle of the SKYMAX Large Panel Slab Formwork with elements made of aluminium and polymer has been expanded since the last bauma to achieve very high technical and economic flexibility for customers with demanding projects. PERI will show how the panels can be combined with each other for optimum slab formwork performance and assembled to form slab tables. It is also possible to add additional panels. All work steps, including the creation of high slabs, high load-bearing bracings as well as solutions for corner balancing, are done from the lower level with system components. Space-saving, foldable pallets are available for transport.
The lightweight polymer panels with particularly durable formlining represent a sustainable alternative to conventional timber solutions. For a transparent construction site and optimised logistics processes, the SKYMAX aluminium panels are also equipped with RFID technology as standard. By scanning the built-in RFID tag with a smartphone or UHF reader, users can uniquely identify and assign the panels and retrieve specific component and product information in the PERI MATERIAL SCAN app.
With the ALPHADECK Panel Slab Formwork, PERI will be presenting a new slab formwork at the bauma especially for customers who want to change from conventional formwork methods to system formwork. ALPHADECK is particularly well-suited for flat slabs with large spans and impresses with an intuitive set-up with minimal need for training. With the slim and practical portfolio consisting of only three basic components, large areas can be formed very quickly from the lower level. The ALPHADECK Drophead, which is used as standard, offers the option of early striking and allows the panels to be installed in both directions simultaneously. And thanks to the ALPHADECK bracing, it is also possible to start shuttering at any point.
Increased safety through new protection systems
With an extended portfolio of safety systems for slab formwork, PERI is also setting new standards in product and workplace safety. At bauma, the formwork manufacturer will show how the new HAMMOCK Safety System works. The safety net serves as collective fall protection when shuttering from above and catches larger falling parts – both when working with MULTIFLEX Girder Slab Formwork and when using precast slabs.
As a supplement to the familiar SKY-Anchor for SKYDECK slab formwork, PERI will also be showing the new, universally applicable SKY-Anchor Universal. This also provides a mobile attachment point for a person with personal protective equipment, and allows the panels to be inserted safely from above. What’s more, it can be used flexibly with other slab formwork, e.g. with MULTIFLEX Girder Slab Formwork and on the already concreted slab.
PERI will also be presenting additional safety components at bauma which offer the customer safety and cost savings in line with particularly high standards. The new PROKIT Alpha Side Mesh Barrier for free slab edges, the safety screen for drop heights of up to 6 m and construction stairs for safe access at heights of up to 5 m round off the safety portfolio.
New innovations for building construction Thanks to innovations in the field of climbing technology, visitors to the PERI exhibition hall can reach the top safely and efficiently. PERI is presenting a special highlight with RCS MAX, the advancement of the proven RCS Rail Climbing System. The new RCS MAX Hydraulic Unit and the new RCS MAX Drive Rails can be easily combined with existing material to optimise the performance of the system. After the première of the RCS MAX in South Korea, the system is now also proving its functionality in the FOUR project in Frankfurt. The Frankfurt skyline will be enriched by an ensemble of four high-rise buildings up to 233 m in height. The use of the RCS MAX significantly increases safety on the construction site, as the decentralised hydraulics allow all platforms to climb synchronously.
The advanced components of the VGK offer new application options in structural and transport engineering. In addition to its use as a cantilevered parapet bracket, the console bracket solution now also scores points as a working platform with flexible use, e.g. on pier heads and complex geometries. The new lightweight working platforms can even be used on forward- and backward-sloping walls. Furthermore, VGK can now also be used as a working platform in building construction. The platform unit is pre-assembled on the ground and then hooked onto the structure. In addition, a reinforcement scaffold can be erected on the closed working platforms. In this way, the work is carried out from a secured position, which eliminates the need for a facade scaffold. The VGK Console Bracket solutions are type-tested. In the spirit of digitalisation in construction, the VGK Design Tool also helps users independently plan and dimension their solution.