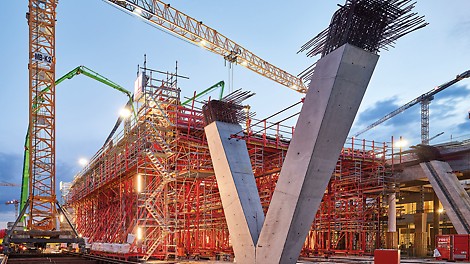

Download Press Release
The images in more detail
The 550-m-long and 27-m-wide drive-by platform with its total bridge area of 15,300 m² is supported by 70 V-shaped columns at a height of over 10 m and connects the two access and departure ramps to the terminal. Engineers from PERI designed a customised formwork carriage for this complex construction project using the VARIOKIT Engineering Construction Kit and the PERI UP Scaffolding Kit as a basis. It was 40 m long, 25 m wide and up to 12 m high – and weighed just under 500 tonnes. The construction process was carried out entirely in 3D.
Lowered hydraulically, repositioned separately
With an integrated hydraulics system, the entire formwork carriage could be lowered by 2.20 m for striking and repositioning. Between the V-shaped columns, the PERI solution was made up of six individual carriages that could be separated for relocation and striking. Outside the V-shaped columns there were two further carriage units that were each 40 m long and could be moved in one piece. For the relocation process in the longitudinal and transverse direction, PERI developed a special hydraulic walking gear that could be transported back and forth between the individual carriage units quickly, easily and manually.
The beams – a separate challenge
The formwork of the oblique-angled and V-shaped beams of the drive-by platform posed a particular challenge. In this case, it was necessary to shutter and strike the beams separately from the formwork carriage – and in a very confined area. This was realised by means of a folding mechanism and the MAXIMO Structure Panel Formwork because of the lower construction height compared to the girder formwork. MAXIMO Structure also made it possible to achieve the desired SB2 architectural concrete class. The beam formwork was operated from a PERI UP Platform located in the belly of the formwork carriage. In order to meet all the occupational safety requirements, all access points and working platforms in the formwork carriage were constructed using the PERI UP Scaffolding Kit.
Faster and safer with excellent documentation
The documentation of the formwork carriage was a key area of focus. In addition to the verifiable structural calculation, which comprised over 1,500 pages, a partly digital operating manual with an independent CE marking was created. QR codes could be scanned to open short video sequences that explained the work steps in detail.
It took more than 16 hours to concrete the first 36-m-long concreting section. All deformations were within the tolerance range. A total of 14 construction phases needed to be carried out to complete the project. The formwork carriage, weighing almost 500 t, was ready to be moved to the next cycle within just one week – almost two weeks faster per concreting section than originally planned.